Our Services
Automation systems require ongoing care to maintain peak performance and prevent costly disruptions.
Automation systems require ongoing care to maintain peak performance and prevent costly disruptions. Regular maintenance is essential to ensure that these systems function optimally, as neglecting them can lead to inefficiencies, unexpected breakdowns, and significant financial losses. By investing in routine checks and updates, organizations can extend the lifespan of their automation systems and avoid interruptions that could impact productivity and revenue. Proper care not only safeguards the system’s operational integrity but also enhances its reliability, ultimately contributing to smoother, more consistent business operations.
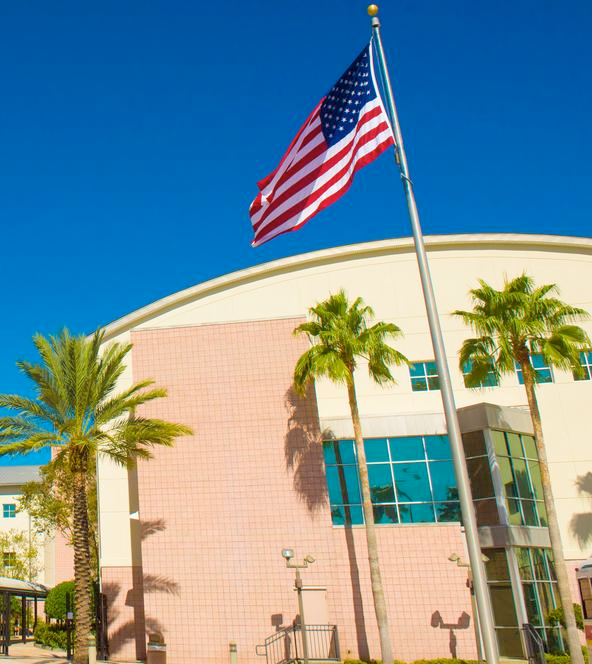
Tampa, Florida
Preventative Maintenance: The Foundation of System Reliability
Regular inspections and maintenance are the cornerstones of a reliable automation system. Through routine checks, we can identify potential issues before they escalate into major problems. Our approach to preventative maintenance includes:
Scheduled System Inspections
We conduct thorough inspections of your automation systems on a regular basis, ensuring that every component is functioning correctly. These inspections help in spotting wear and tear, software glitches, or any other anomalies that could lead to system failure if left unaddressed.
Component Upkeep
By maintaining the various components of your automation system—such as sensors, actuators, controllers, and communication networks—we ensure that each part operates smoothly. This proactive approach helps in extending the lifespan of your equipment and reducing the likelihood of unexpected breakdowns.
Data-Driven Predictive Analysis
Leveraging the power of data, we use predictive analytics to anticipate potential failures before they occur. This allows for timely interventions, saving both time and money while enhancing system reliability.
Equipment Repair: Minimizing Downtime with Swift Responses
Despite the best preventative measures, equipment malfunctions can still occur. When they do, swift and effective repairs are essential to minimize downtime and keep your operations running smoothly. Our approach to equipment repair includes:
Rapid Response Teams
Our expert technicians are always on standby, ready to respond to any equipment failure. With a deep understanding of automation systems, they can quickly diagnose issues and implement solutions to get your system back online with minimal delay.
Root Cause Analysis
Beyond just fixing the immediate problem, we conduct a thorough root cause analysis to understand why the failure occurred. This enables us to address the underlying issue, preventing similar problems from arising in the future.
Cost-Effective Solutions
Early detection of issues not only prevents larger, more complex problems but also reduces the overall cost of repairs. By addressing malfunctions promptly, we help you avoid the expensive consequences of prolonged downtime and extensive damage to your equipment.
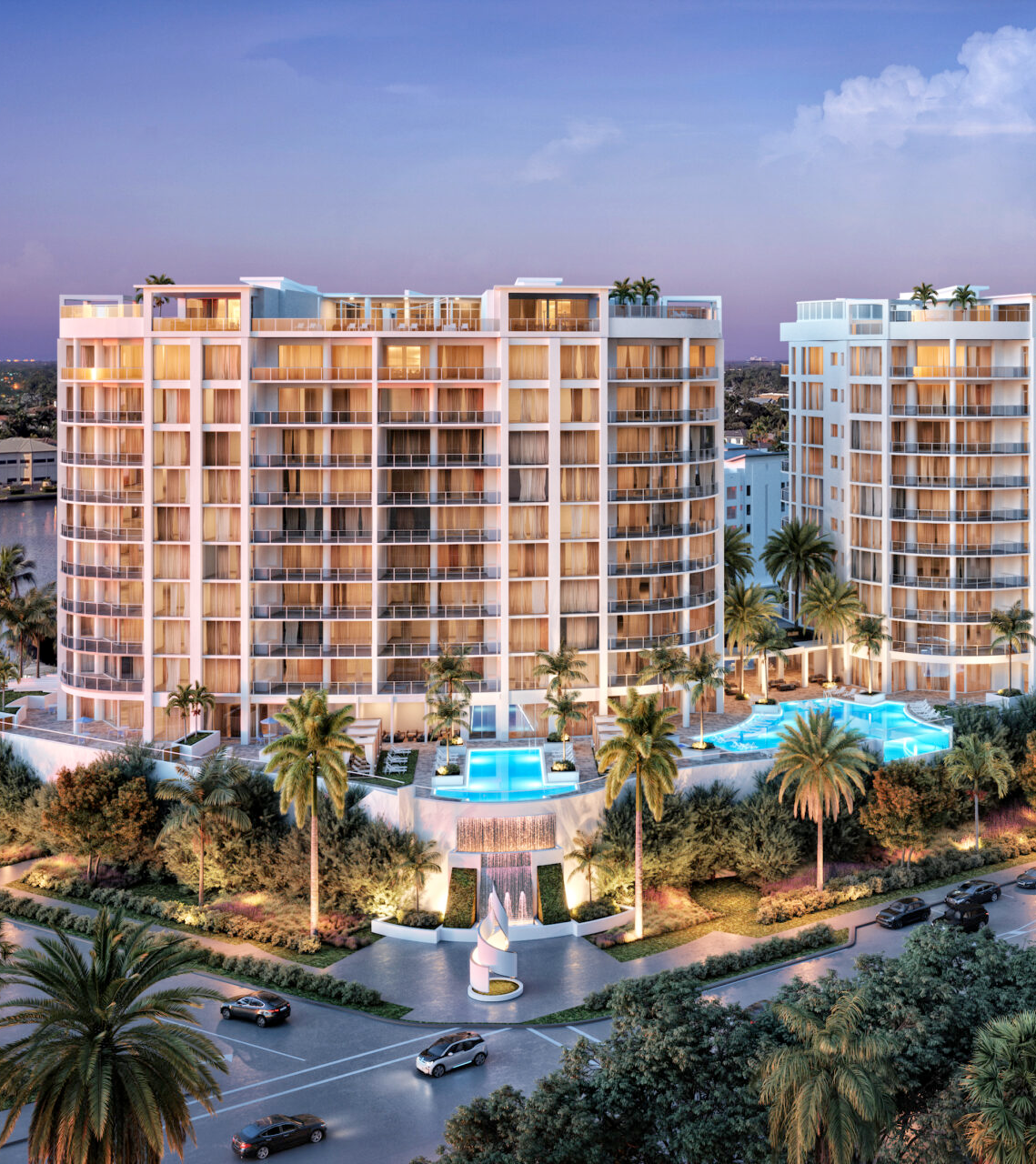
Naples, Florida
Continuous Improvement: Adapting to Evolving Needs
Automation technology is constantly evolving, and so are the demands on your systems. To ensure your automation systems remain up-to-date and capable of meeting your operational needs, we also focus on:
System Upgrades
As new technologies and software updates become available, we assist with upgrading your systems to incorporate these advancements. This keeps your operations at the cutting edge and enhances performance.
Training & Support
We provide ongoing training for your team to ensure they are fully equipped to operate and maintain the automation systems effectively. Our support services are also available whenever you need assistance, ensuring you’re never left without the help you need.
We are a proud provider of
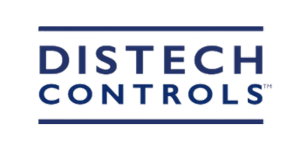
let’s talk
about your next project.
Discover the TekPlan Solutions difference.